标准的电动汽车 (EV) 汽车电池可以分解为电池级别、模块级别和电池组级别。电池主要包括阳极和阴极,模块包括多个电池,电池组包括多个模块。
锂离子电池组中最常见的三种金属对金属接头是箔对极耳、极耳对极耳和极耳对母线。所有三个接头都带来了连接挑战,但在这三个接头中,将多层箔片焊接到接头上是最具挑战性的。接头通常由不同的金属制成,并且金属厚度不匹配。翼片相对较厚(例如,0.2 毫米),而多个箔极薄(例如,0.025 毫米)。下图显示了大幅面锂离子袋式电池的示意图。
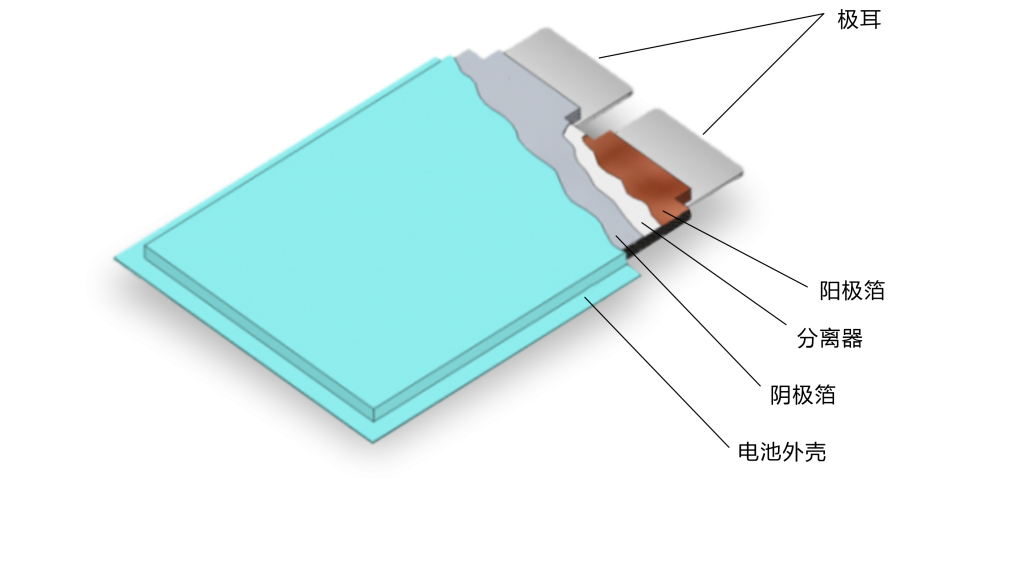
需要箔对极耳焊接来收集电池内部的所有阳极和阴极箔,并将它们连接到从电池外壳伸出的极耳,从而使电池的能量能够转移到外部来源。每个电池中有两个箔片焊缝,典型的大型锂离子电池组中有数百个电池。由于串联和并联连接,箔片接头中的一个故障将影响整个电池组的输出。因此,需要一种稳健的连接工艺来满足连接要求,例如在连接不同材料时令人满意的连接强度、低电阻连接和最小的金属间层。
针对此特定应用评估了超声波金属焊接 。该过程的示意图如下所示。超声波金属焊接能够焊接电池相关材料(例如铜、铝和镍)的相似和不同组合。超声波振动,通常为 20 到 40,000 赫兹,用于在压力下将两个部件摩擦在一起。擦洗动作可去除表面上的氧化物和污染物,并打破表面粗糙,形成两个光滑、干净的金属表面。一旦它们在适度的热量和压力下接触,就会形成焊缝。
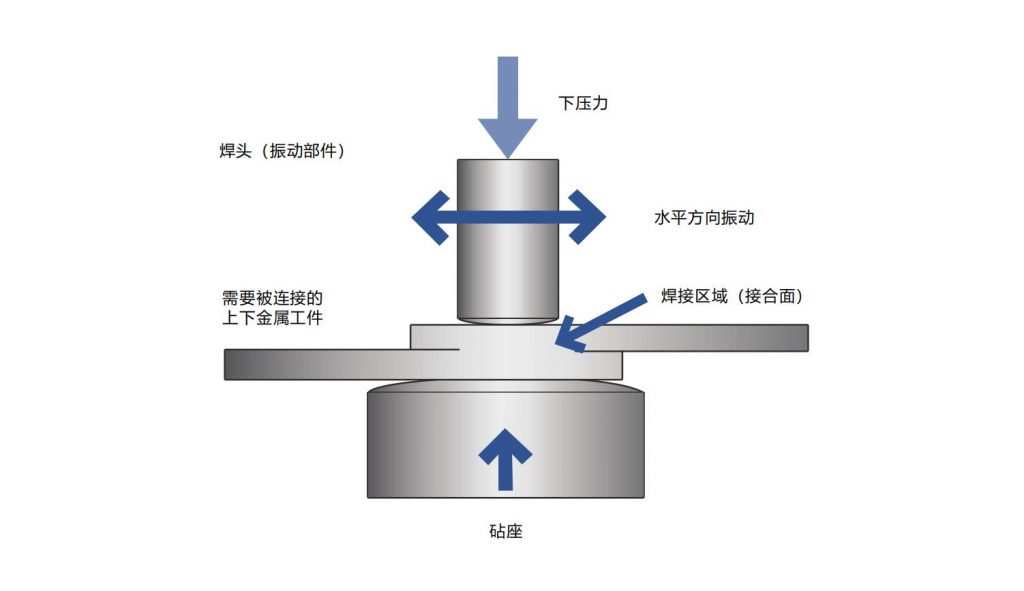
该过程有几个优点。由于它是一种固态工艺,因此可以适应不同的材料组合,并避免了对金属间化合物形成的大部分担忧。它非常适合焊接电池中使用的高导电材料,包括镀铜和镀铝。它不需要高功率,焊接周期非常短,只有几分之一秒。它还可以在一次操作中连接多层薄材料,并提供具有低电阻的高强度连接。
也有其他连接工艺,包括焊接、磁脉冲焊接、电阻点焊和激光束焊接,但它们缺乏某些特性,超声波金属焊接成为多层箔到极耳应用中更理想的连接工艺。
- 焊接可用于连接软包电池片。它特别适用于连接不同的材料,但使用助焊剂会增加腐蚀的机会,这会直接影响接头的强度。
- 磁脉冲焊接可以提供高强度的接头,但该过程会产生较大的变形,感应电流可能会损坏电池的内部组件。请注意,磁脉冲焊接在电池组件中的应用正在研究中,因此,该技术尚未准备好供电池制造商使用。
- 电阻点焊依靠材料的电阻来产生用于连接的热量。然而,通常用于电池行业的铝箔和铜箔具有极低的电阻。此外,铝合金会形成一层坚韧的表面氧化层,这会抑制 电阻点焊,并且由于氧化层存在于每个箔层的两侧,这一事实进一步加剧了这种情况。
- 激光束焊接对焊缝中材料层之间的间隙非常敏感。一般来说,间隙应小于材料厚度的 10%。连接 12 µm 的箔片需要 1.2 µm 或更小的间隙,这很难实现并且需要过多的夹具。激光束焊接的另一个问题是反射材料使用的敏感性。
- 超声波金属焊接不依赖于体电阻,并且作为工艺的一部分固有地清除氧化物层。因为超声波金属焊接是自夹紧的,所以间隙不是问题。此外,声波金属焊接工艺对反光材料不敏感。
典型的大型锂离子电池使用铜箔作为阳极集电器,铝作为阴极集电器;因此,铜和铝都使用超声波金属焊接工艺进行了评估。如上图所示,实验接头仅限于类似的材料堆叠,这意味着铝箔连接到铝片,铜箔连接到铜片。接片厚度保持在 0.127 mm 不变。评估了两种箔厚度,0.012 和 0.025 毫米,以及两种箔堆叠高度,20 层和 60 层,以证明可行性,并研究随着箔厚度和箔层数的变化对接头性能的影响。
横截面 – 20 层薄铜箔到铜片 横截面——60层厚铝箔到铝片 对上述横截面的分析提供了对箔片压缩、箔片损伤和焊接接头最终状态的更深入了解。具有更薄和更少箔层的样品显示出直接靠近焊接区的箔移动增加。相比之下,具有更厚和更多箔层的样品显示出邻近焊接区的箔的固结,通常导致更大的结合区域。粘结区域的固结和增加是因为较厚的箔堆叠在焊接工具上触底,导致焊接区域附近区域的压缩。
在单个超声波金属焊接操作中将多层薄箔连接到极耳是可行的。可以在不破坏脆弱的箔层的情况下实现焊接。粘合发生在箔片到接头的界面以及每个箔片到箔片的界面,从而形成坚固、高导电的机电接头。这种被认为是低能耗工艺的工艺可以用于在几分之一秒内连接不同的材料。