铝合金熔体净化处理是获得高质量熔体的有效途径 之一,也是提高铸造铝合金综合性能的有效手段。 铝合金熔体净化处理的诸多方法中,功率超声除气方法作为一种经济环保、效果明显的方法,已经得到世界上 各国的广泛关注,是目前铝合金除气方法中的研究热点 之一。旋转喷吹除气方法作为一种高效除氢技术被国内 外所公认,并受到大量使用者的欢迎。但目前仅采用单 一的除气方法仍难以达到日益提高的工业要求所提出的净化效果,无法满足航空航天领域的较高要求,为此,可尝试采用两种或两种以上的方法复合除气。 本文将对铝合金熔体旋转喷吹及功率超声复合式除 气过程进行模拟分析,尝试将两种除气方法进行复合, 希望从各种角度加深对复合除气方法除气过程的认识, 以期能够提升和优化现有铝合金熔体净化技术。
试验模拟方法
为了了解铝合金熔体旋转喷吹及功率超声复合除气 方法除气过程,采用计算机模拟方法对不同除气方法、 不同工艺条件下铝合金熔体内部压力分布进行了研究。
首先创建几何模型,建立的三维模型包括熔池槽模 型和旋转喷头模型,模型计算域利用 Gambit建立, 寸参照实验设备尺寸。熔池槽模型采用圆柱形熔池槽, 槽高为 300mm,半径为 200mm。旋转喷头模型包括 旋转喷头组件模型和旋转轴模型,旋转喷头组件距熔池槽30mm,旋转喷头底盘由六个奖叶实体构成,旋 转喷头底盘最大半径为 90mm,厚为 60mm,转喷头 底盘上设有 6 个半径为4mm 的圆形气流出口,旋转轴半径为 45mm。为了使用多重参考系(MRF),将流体区域用高为 100mm,半径为 100mm 的圆柱体划分为两 个部分:外部流场和旋转流场。外部流场采用静止参考 系旋转流场使用以桨叶速度旋转的运动参考系。然后创建网格模型,模型包括旋转流场模型和外部流场模型, 模型仍利用 Gambit 建立。旋转流场由于靠近旋转轴, 旋转速度较快,因此旋转流场的网格应比外部流场的网 格更密,网格间距设置的更小,创建的单元总数为291066。
最后利用 Fluent 导入网格模型,工作条件参考压 力为 101325Pa,重力加速度为9.81m/s’。计算模型 采用非稳态三维两相流混合模型,粘性模型采用标准 k-e 模型,壁面函数采用标准壁面函数法。
按照 HB5480-91的规定,配得实验材料 ZL114A 铝合金,其合金化学成分如表1所示。
仿真模拟的是 700C温度下的 ZL114A 铝合金熔体的情况,因 此需要高温下的热物性参数。本 文ZL114A 铝合金熔体的密度、 粘度参数通过 PrOCAST 热力学 数据计算获得,ZL114A 物性参 数如图1所示;气的密度、粘度参 数通过 FIuent 材料库获得。 700℃温度下的材料参数设定, 主相为铝合金熔体,密度为 2394kg/m,动力粘度为 1.2X10Pas;第二相为气,密度为 1.6228kg/m,动力粘度为 2.125X10Pas。
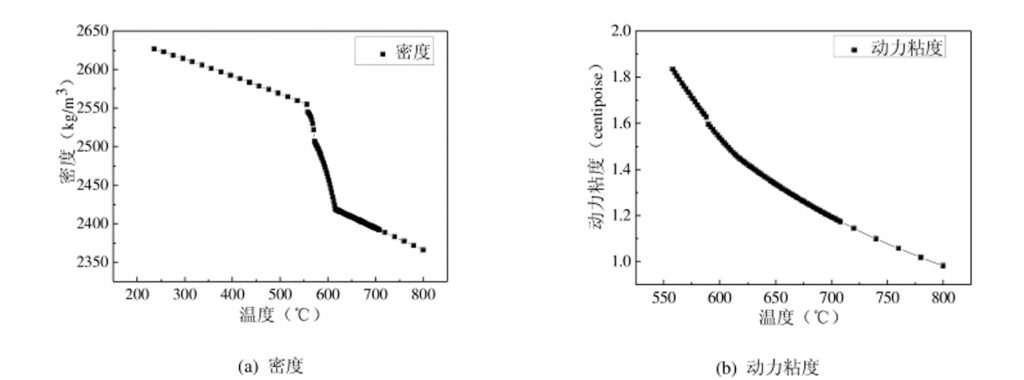
仿真模拟过程中假设气体是不可压缩的,铝合金熔体和气的动力粘度为定值。离散格式选择阶迎风格式离散,求解选择分离式求解方法,其他保持系统默认设置即可。时间间隔从 0.001s 开始, 逐渐递增,每时间间隔内最大迭代次数为 30。对熔池槽选取 Y=O 面,即沿旋转轴的纵截面观察模拟结果。
试验结果与分析
为了了解不同除气方法对除气过程内部流场的影响,分别进行单一 旋转喷吹除气方法下除气过程内部流场的模拟和旋转喷吹及功率超声复 合式除气方法下除气过程内部流场的模拟。单一方法的工作参数中旋转 喷头转速为 300rpm,喷头底盘上气流出口的气体速度为 0.2m/s。复 合方法中旋转喷吹工作参数与单一方法中相同,功率超声工作参数通过 编写 UDF 程序的形式设置动网格,模拟超声波变幅杆端面振动。功率 超声工作参数中变幅杆端面振动频率为 20000Hz,振幅为 10um。复 合除气方法模拟是首先进行单一旋转喷吹除气方法模拟的试验,然后添 加瞬时超声(t=5X 10s,t代表步长).通过模拟得到的内部压力分布流场。 试验结果如图 2 所示。
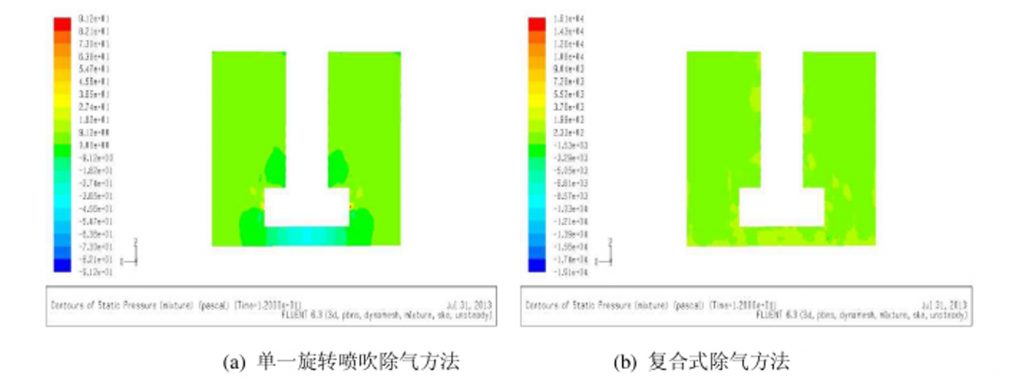
经分析可以得出:单一旋转喷吹除气方法下沿旋转轴的纵截 面的压力分布,见图 1a,旋转轴周围熔体的压力分布不大, 而远离旋转轴即靠近圆柱形熔池槽壁面周围熔体的压力分布 却较高。由旋转轴向熔池槽壁面方向呈逐渐增强趋势,压力 差的存在导致气泡向熔池槽中心偏聚,降低了气泡与远离旋 转轴熔体的接触,不利于除气。同时也可以看出,在旋转喷 头底盘下面压力很低,是一个低压区,容易吸气。也就是说 在除气过程时旋转喷头底盘下方最容易聚集气体,且不能快 速逸出,这对铝合金旋转喷吹除气法的除气效率的提升有很 大阻碍作用。旋转喷吹及功率超声复合式除气方法下沿旋转 轴的纵截面的压力分布,见图 1b,旋转轴周围熔体的压力 一定区域内压力较大,远离旋转轴的压力分布相对较小,此 压力差有利于气泡向熔池槽壁面方向运动,增加气泡与熔体 的接触,有利于除气。同时旋转喷头底盘下的低压区在旋转 喷吹与超声共同作用下消失,避免了气体的聚集所以与单一 旋转喷吹除气方法相比,旋转喷吹及功率超声复合式除气方 法改善了气泡在熔体中的分布,有利于气泡与熔体的接触和 气体的逸出,提高熔体除气率。
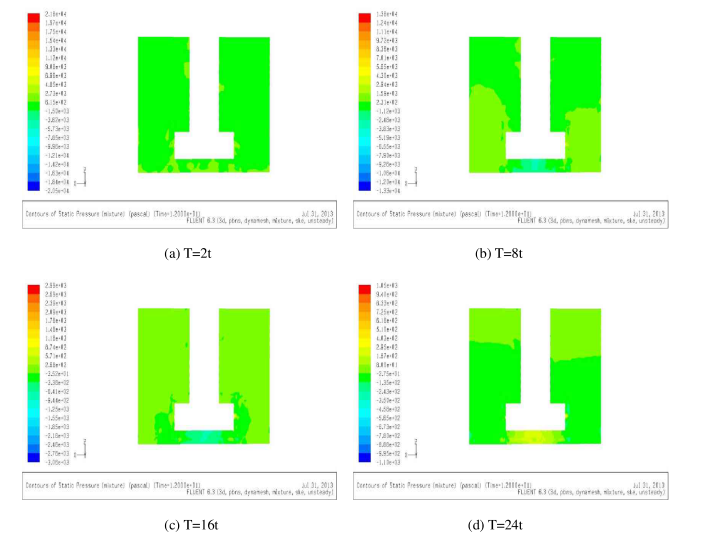
为了了解超声作用时间对复合式除气方法除气过程内部流场的 影响,选定旋转喷头转速为 300rpm,喷头底盘上气流出口的 气体速度为 0.2m/s,变幅杆端面振动频率为 20000Hz,变幅 杆端面振幅 10um 的情况下进行超声作用时间分别为 2、8t、 16t、24t 时进行模拟试验。试验结果如图3所示。
由图 3 分析可以得出,作用时间为 2t 时,压力分布呈现旋 转轴附近压力大于远离旋转轴区域,压力差有利于气泡向熔 池槽壁面方向运动,有利于气体与熔体接触和气体的逸出, 此时动边界上升速度较大,超声的作用大于旋转喷吹作用: 作用时间为 8t、16t 时,旋转喷头底盘下方的低压区重新出 现,容易引起气体聚集,且随着作用时间的增长低压区逐渐 增大。此时由于动边界上升阶段速度逐渐降低,在低于某临 界速度后旋转喷吹的作用更为明显,导致气体向低压区聚集, 但同时加大了气体在熔体中的运动;作用时间为 24t 时,熔池 槽下部形成较大低压区,而旋转喷头底盘下方形成相对高压 区,压力差导致气体又向周围熔体运动。当 T>24t 后,动边 界运动将转为下降阶段,熔体内部流场随振动作用时间的变 化刚好与上升阶段相反,如此上升阶段与下降阶段交替进行, 对气泡在熔体中的运动起到促进作用。相比单一除气方法熔 体内部流场较为稳定的压力梯度,由于振动和旋转喷吹对熔 体的共同作用,在超声作用时间逐渐增加的情况下,熔体内 压力变化明显,这种明显的压力变化有效改善气泡在熔体中 的分布并加剧气泡在熔体中的运动,更有利于气体与熔体的 充分接触,提高熔体除气率。
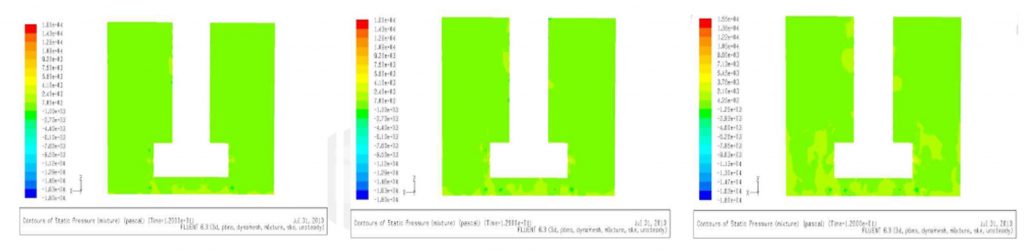
为了研究功率超声振幅对复合式除气方法除气过程内部流场的 影响,选定旋转喷头转速为 300rpm,喷头底盘上气流出口的 气体速度为 0.2m/s,变幅杆端面振动频率为 20000Hz 的情 况下考察变幅杆端面振幅分别为 10um、15 m、20 时相同作 用时间下进行模拟试验。试验结果如图 4所示。
从图 4 中可以看到,不同振幅的功率超声与旋转喷吹共同作用 下熔体的压力分布呈现旋转轴附近压力大于远离旋转轴区域, 压力差有利于气泡向熔池槽壁面方向运动。振幅在一定范围内, 振幅越大,动边界上升阶段速度越大,旋转轴周围高压区的面 积越大,与低压区的压力梯度也越大,在实际除气过程中我们 也希望这种压力差较大的压力分布,这样更有利于气泡向熔池 槽壁面方向运动,有利于气体与熔体的接触。因此超声的振幅 对铝合金熔体旋转喷吹及功率超声复合式除气过程内部流场具 有重要影响,振幅在一定范围内,振幅越大,越有利于改善气 泡在熔体中的分布,提高熔体除气率。
实 验 结 论
(1) 旋转喷吹及功率超声复合式除气方法除气过程中压力分布比单一旋转喷吹除气方法在除气过程中压力分布有优势,有利于气体与熔体的接触和气体的逸出。
(2) 旋转喷吹与超声共同作用时间越长,越有利于气体与熔体的充分接触。
(3) 旋转喷吹与超声共同作用时的超声振幅越大,越有利于改善气泡在熔体中的分布。